L’importance du choix des gaz de protection en soudure d’aluminium
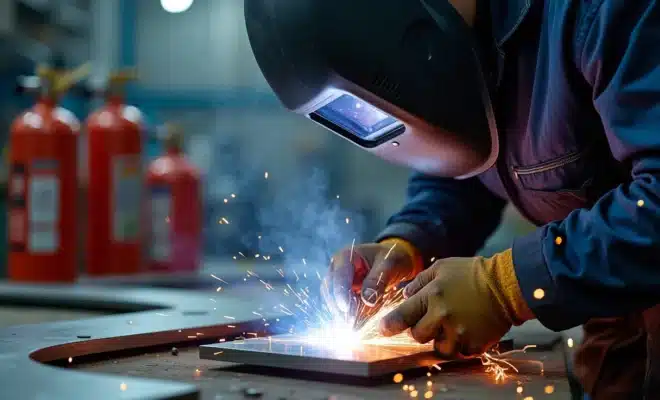
Le soudage de l’aluminium pose des défis uniques en raison de ses propriétés particulières, telles que sa conductivité thermique élevée et sa réactivité avec l’oxygène. Lors de ce processus, le choix des gaz de protection joue un rôle fondamental pour garantir une soudure de qualité.
L’argon, souvent utilisé, offre une protection efficace contre l’oxydation et aide à stabiliser l’arc de soudure. Pour des soudures plus complexes, l’ajout d’hélium améliore la pénétration et la vitesse de soudage. Un mauvais choix de gaz peut entraîner des défauts tels que des porosités ou des fissures, compromettant ainsi la solidité et la durabilité des assemblages.
A lire en complément : Comment le Storytelling peut augmenter les ventes de votre entreprise
Plan de l'article
Rôle du gaz de protection dans le soudage de l’aluminium
Le gaz de protection est essentiel pour protéger l’aluminium pendant le processus de soudage. Ce métal, particulièrement réactif, nécessite un environnement contrôlé pour éviter la formation d’oxydes qui compromettent la qualité de la soudure.
Gaz de protection comme l’argon et l’hélium servent à protéger l’aluminium des contaminations atmosphériques. Ces gaz inertes créent une atmosphère stable autour de la zone de soudage, réduisant les risques de défauts.
A lire également : Comment réaliser une adjonction d'activité ?
Le soudage MIG (Metal Inert Gas) et le soudage TIG (Tungsten Inert Gas) sont des procédés couramment utilisés avec des gaz de protection pour souder l’aluminium. Ces techniques permettent de maintenir l’arc électrique stable et de contrôler la fusion du métal d’apport.
- Le soudage MIG utilise généralement de l’argon pur ou un mélange argon-hélium, offrant une bonne pénétration et une vitesse de soudage accrue.
- Le soudage TIG, quant à lui, privilégie souvent l’argon pur pour la précision et la propreté de la soudure.
La sélection du gaz de protection pour le soudage de l’aluminium dépend de nombreux facteurs, y compris le type de soudage, l’épaisseur du matériau et les exigences de la soudure finale. Le choix judicieux de ces gaz est déterminant pour obtenir des soudures de haute qualité, exemptes de porosités et de fissures.
Critères de sélection des gaz de protection pour l’aluminium
Le choix des gaz de protection pour le soudage de l’aluminium repose sur plusieurs critères déterminants. La nature du gaz utilisé influence directement la qualité et les propriétés de la soudure. Parmi les gaz couramment employés, on retrouve :
- Argon : ce gaz inerte est largement utilisé pour le soudage TIG et MIG. Il offre une excellente protection contre l’oxydation et permet un arc stable.
- Hélium : souvent mélangé à l’argon, il améliore la pénétration de la soudure et augmente la vitesse de soudage. Toutefois, son coût plus élevé en limite parfois l’utilisation.
- Dioxyde de carbone : généralement utilisé en petites quantités dans les mélanges pour améliorer la stabilité de l’arc.
- Oxygène : ajouté en faibles proportions pour améliorer la fluidité du bain de fusion et l’humectabilité.
- Hydrogène : peut être utilisé pour améliorer la pénétration et la stabilité de l’arc, mais doit être employé avec prudence en raison de son potentiel à causer des fissurations.
Considérez aussi l’épaisseur du matériau à souder. Pour les pièces fines, l’argon pur est souvent privilégié pour sa stabilité et sa propreté. Pour les pièces plus épaisses, un mélange argon-hélium peut offrir de meilleurs résultats en termes de pénétration et de vitesse de soudage.
Le coût des gaz de protection est un autre facteur à prendre en compte. Si l’argon reste le choix standard, l’ajout d’hélium, bien que bénéfique, augmente les coûts. La sélection doit donc équilibrer performance et budget.
La composition des mélanges de gaz doit être adaptée aux spécificités de chaque projet de soudage. Une compréhension approfondie de ces critères permet d’optimiser les résultats et de garantir des soudures de qualité.
Comparaison des différents gaz de protection pour le soudage de l’aluminium
Lorsque l’on compare les différents gaz de protection pour le soudage de l’aluminium, plusieurs aspects doivent être pris en compte. Chaque gaz possède des propriétés spécifiques qui influencent le résultat final du soudage.
Argon : L’argon est le gaz de protection le plus couramment utilisé en raison de sa capacité à offrir une protection stable et efficace. Il convient particulièrement aux soudures de faible épaisseur et assure une protection contre l’oxydation.
Hélium : L’hélium, souvent mélangé à l’argon, améliore la pénétration de la soudure et augmente la vitesse de soudage. Il est particulièrement adapté pour les pièces plus épaisses. Son coût plus élevé peut constituer un frein à son utilisation généralisée.
Dioxyde de carbone : Le dioxyde de carbone, utilisé en petites quantités dans les mélanges, stabilise l’arc et améliore la fluidité du bain de fusion. Toutefois, il peut provoquer des projections et n’est pas recommandé pour les soudures fines.
Oxygène : L’oxygène, ajouté en faibles proportions, améliore la fluidité du bain de fusion et l’humectabilité. Son utilisation doit être équilibrée pour éviter toute oxydation excessive.
Hydrogène : L’hydrogène, bien que potentiellement bénéfique pour améliorer la pénétration et la stabilité de l’arc, doit être utilisé avec prudence en raison de son potentiel à causer des fissurations.
Gaz | Propriétés | Applications |
---|---|---|
Argon | Protection stable, prévention de l’oxydation | Soudure de faible épaisseur |
Hélium | Amélioration de la pénétration et vitesse de soudage | Soudure de pièces épaisses |
Dioxyde de carbone | Stabilisation de l’arc, amélioration de la fluidité | Mélanges pour stabilisation |
Oxygène | Amélioration de la fluidité du bain de fusion | Mélanges pour humidité |
Hydrogène | Amélioration de la pénétration, stabilité de l’arc | Utilisation prudente pour éviter fissurations |
La sélection du gaz de protection doit être adaptée aux spécificités de chaque projet de soudage. Une compréhension approfondie de ces critères permet d’optimiser les résultats et de garantir des soudures de qualité.